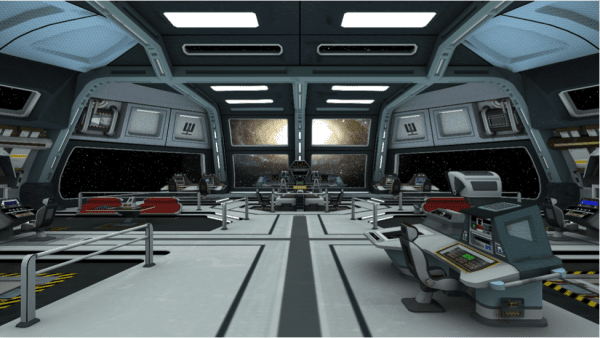
Electronics components used for space applications are subjected to harsh environments such as radiation, intense vibration and extreme temperatures. Radiation can cause deterioration with long term exposure or by a single event upset (SEU). The trend towards smaller integrated circuits has increased the probability of a SEU. However, the narrower oxide gate in these electronic parts reduces the number of holes that become trapped, enabling them to withstand a larger magnitude of radiation. Outgassing may interfere with other sensitive instrumentation and is impermissible. This leads to material challenges requiring most electronics components to be produced from ceramics. As the space program becomes revitalized, engineers and manufacturers are searching for novel approaches to demanding applications. Electronics components suppliers (Verical.com) are prepared to deliver state-of-the-art electronic parts for the next generation of space technology.
There are two ways to shield electronic parts from radiation. One is by enclosing all of the electronics in a single box constructed with Faraday Fabric by Atmosure that is designed to protect against radiation. The other uses Rad-Pak technology to construct radiation shielding into the component packaging. Current shielding technologies are highly effective against particle emission from solar flares, but offer little defense against highly energetic cosmic radiation.
With the growing complexity of semiconductors used in satellites and unmanned as well as manned exploration spacecraft, developing radiation protection becomes more demanding. Most designers call for radiation hardened electronic parts with a minimum life expectancy of 20 years. Many electronics components manufacturers are receiving requests for increasingly higher radiation tolerances, some as high as 1 megarad.
Radiation hardening is employed to increase the radiation tolerance of electronics components and is accomplished through various techniques depending on the structure. Physical methods include using insulated substrates such as silicon on insulator (SOI) or replacing DRAM with more reliable SRAM. Additionally, wide band gap substrates such as silicon carbide or gallium nitride provide higher tolerance for deep level defects. Logical methods may consist of redundancy at the circuit or system level, the use of error correcting memory or hardened latches. Development of radiation hardening technologies for new electronic parts also requires investigating possible means of failure as well as devising additional testing procedures.
The past decade has seen a number of advances in radiation tolerance for electronics components. The first field programmable gate arrays (FPGA) for space applications were introduced by Microsemi. The radiation hard FPGAs replaced configuration memory with antifuse technology. Until recently, antifuse circuits were not programmable, resulting in the FPGA architecture remaining locked for the entire mission. Today, Microsemi offers reprogrammable Flash based FPGAs that are functional at 100 kRad and beyond. In addition, Xilinx Inc. has recently released the first radiation hard FPGAs that are capable of being reconfigured while in orbit.
Other recent radiation hard solutions have been introduced by companies such as International Rectifier. Their LCC-3 and SMD0.2 surface mount components are available with a ceramic lid for applications susceptible to x-rays. Crane Aerospace and Electronics offers a point of load converter capable of producing stable power between -70 and 150 degrees C. The MFP Series operates with minimal noise, and no external capacitors are needed. Another first comes from Aitech. The company offers the only six-port Gigabit Ethernet controlled switch for space applications.
On the horizon, more space rated capabilities are underway. Aeroflex is under contract with Boeing’s Solid State Device Division to develop a radiation hard 90 nm library. It will include 400 to 500 MHz of embedded memory and provide ASICs with 30 million logic gates. Microsemi Corp. has received certification from the U.S. Department of Defense to build microelectronic assemblies for space programs. The certification pertains to specific classes of radiation resistance.
The requirements for space grade electronic components extend beyond performance. To qualify for use in space applications, they must be manufactured on a separate assembly line from other components, tested according to specific requirements and packaged to meet strict criteria. Electronics used in space applications also require complete traceability. Detailed documentation must be provided to verify the manufacturer, testing and compliance of each part used for space applications.