We live in a world that is dominated by machines. We use them in every aspect of our day to day lives, and never more so than in the manufacturing field. Every day, hundreds of thousands of machines are operated, either by computer processes (such as CNC machines) or by hand (lathe machines and so on).
Professional help is needed
These are all extremely high-powered, and therefore could be very dangerous if they aren’t made compliant to certain safety standards set down by the industry. The problem is that a lot of owners don’t bother subjecting their machinery to the right risk assessment procedures. This can lead to a whole lot of problems later on, the least of which is the possibility of a large lawsuit.
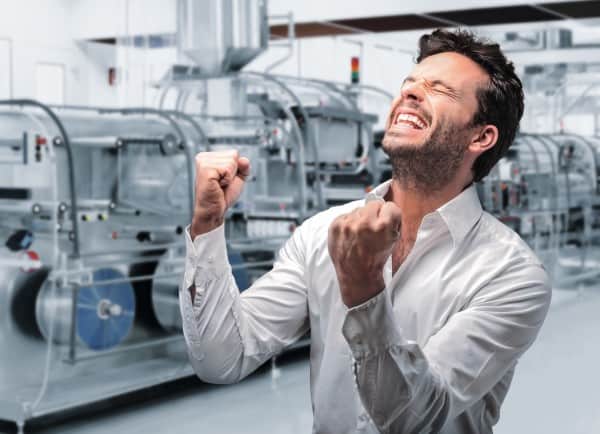
However, this analysis of the risk involved in a machine can easily be done by consulting with professionals who specialize in this sort of procedure. The basic steps to checking if a machine or a unit is safe for handling are easy enough to learn and do on your own as well, although it is always advisable to consult with a professional.
Two of the many basic steps are:
Identification
This is the first step to performing a good analysis of machine risk. It is also one of the easiest, especially when the machines in a factory have been used for a while. A simple review of the number of accidents or close calls occurring with each machine will give a good insight into which machines bring the highest risk and need to be dealt with sooner rather than later.
In addition to this, using common sense is also advised. A good example is that it is basic knowledge that a hand-operated machine poses a greater risk than one that is driven by a computer program. Case in point, a lathe machine operator is far more susceptible to near-fatal injury through a mistake being made than a CNC programmer.
While all machines have risks attached to them, it can’t be denied that some are greater than the others. The standard way to go in cases like this is to reduce the risks attached to the high-risk machinery first, and then move down the list to the lowest.
Information gathering
This is the second step and is one of the most crucial when it comes to the assessment of the level of risk of a certain machine or manufacturing process. All of the information related to the machine has to be collected from multiple sources. Information is the life blood of any operation within a company, and it has never been more important than right now. Amplify the safety by using safety management systems.
The data collected includes the limits of the machine and its requirements, as specified by the manufacturer. All design drawings, descriptions and sketches are collected as well. The incident history of the machine is taken too, which is basically a report of all the accidents or near misses that the machine’s operators have had over the lifetime of the machine.