Concrete temperature monitoring is an important aspect of concrete construction and safety. Installing temperature sensors in concrete allows contractors and engineers to track the temperature of concrete from the time of placement through curing. Monitoring concrete temperatures ensures that the concrete cures properly and reaches the desired strength. What are some key reasons to use temperature sensors in concrete?
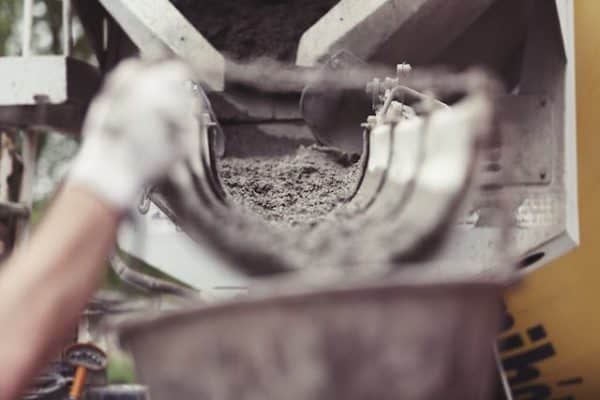
Monitoring Heat of Hydration
The heat generated as concrete cures, known as the heat of hydration, is a critical factor in proper concrete curing. If the temperature rises too quickly, it can cause cracking or other defects. A temperature sensor for concrete allows contractors to monitor the heat and take steps like using chilled mixing water or scheduling placements for cooler weather if the temperatures are rising too rapidly.
Tracking Strength Gain
The strength of concrete increases most rapidly during the first few days after placement. Concrete gains strength slowly as a function of temperature. Sensors provide data on concrete strength gain so engineers know when forms can be removed, when post-tensioning can be done, and when the structure may be put into service.
Avoiding Thermal Shock
If temperatures change too drastically such as rapid cooling in cold weather, the differential temperature in the concrete can cause cracking and other issues. Gradual temperature changes are important. Temperature data enables contractors to take steps to avoid thermal shock, like using insulation or heating to manage the rate of temperature change.
Monitoring Freeze-Thaw Conditions
Temperature sensors help monitor for freeze-thaw conditions which can damage concrete. If temperatures drop below freezing, data from the sensors inform decisions on using insulation or heating to protect the concrete.
Early Warning of Potential Defects
The temperature data from sensors allows early identification of potential issues. Rapid hydration, expansion at joints, or freezing can be detected and addressed before defects form.
Safety Monitoring
Monitoring for conditions like rapid hydration and expansive reactions improves worksite safety by enabling contractors to respond promptly if problems arise.
Temperature Sensor Options
- Thermocouples – These instruments are inexpensive sensors consisting of two wires of different metals welded at the ends. They produce small voltages related to temperature.
- Thermo Resistance Temperature Devices (RTDs) – These sensors use electrical resistance in metals to measure temperature. RTDs provide accurate, stable temperature measurements.
- Infrared Thermometers – These devices measure the surface temperature of concrete using infrared radiation. They quickly measure temperature at many points.
- Wired Temperature Sensors – These contain a temperature probe connected to a data logger or monitoring system via wiring. Wired sensors allow for real-time, continuous monitoring.
- Wireless Sensors – These tools use radio transmitters to send temperature data to a receiver. They do not require wiring installation.
To get the most useful temperature data, the sensors should be installed in the proper positions within the concrete pour. Typical placement locations include near the surface, the middle, and the bottom of the slab or wall. Multiple sensors may be needed for larger pours or to monitor different areas. The temperature data is then collected by data loggers or monitoring systems and analyzed to ensure proper concrete curing and prevent defects.
Installing temperature sensors in concrete is an important technique for monitoring curing and ensuring high-quality concrete construction. The temperature data provides insights into concrete conditions during the curing process. Various sensor options are available, and proper placement within the poured concrete allows monitoring of temperatures throughout the slab during the critical curing phase.