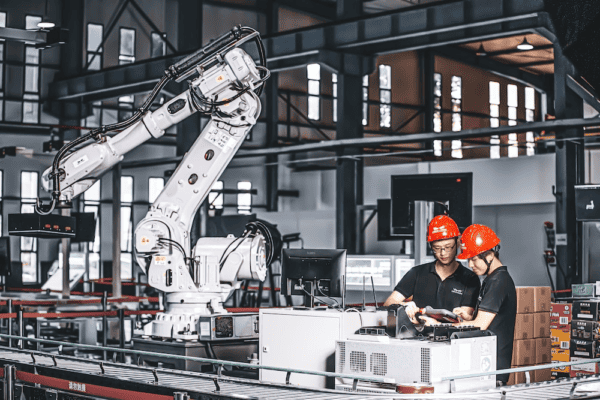
Manufacturers who want to stay ahead of the competition must consistently improve their manufacturing processes to avoid delays and other needless problems. Improving the manufacturing process and workflow will reduce downtime and improve a company’s bottom line.
What Is Process Improvement?
Process improvement in manufacturing is an umbrella term that covers several actions, including optimizing every workplace task to ensure increased efficiency and productivity. Many manufacturers now use MRP software solutions to help them improve their operations. Companies cannot embrace process improvement without evaluating their operations first. Companies first need to define the way they do business, and then they must make integral changes to achieve refinement.
Effective Process Improvement Techniques for Manufacturers
Manufacturers have many options for implementing process improvement techniques. Process improvement is critical for helping manufacturers see significant profit increases. Without improvements, manufacturers could experience sales losses, increased expenses, and missed opportunities. Thankfully, there are ways manufacturers can implement process improvement without headaches.
The Six Sigma Method
A scientist at Motorola developed the Six Sigma method in the 1980s. The Six Sigma method uses statistical data to reduce imperfection variables in manufacturing. There are five aspects to this process improvement strategy.
- Defining
- Measuring
- Analyzing
- Improving
- Controlling
There is also the Lean Six Sigma method. This process is slightly different and helps reduce wasted resources, time, effort, and skill. With this method, manufacturers label any resource that provides no value for the end user as waste.
The Lean Manufacturing Method
Lean manufacturing, often referred to as lean production, identifies seven areas of waste and seeks to eliminate them. Manufacturers should consider the following steps in this method.
- The transportation of materials and products
- The movement of tasks within the facility
- Time spent between tasks
- Production processes that prove invaluable to the end product
- Production of products despite low demand
- Time wasted correcting unnecessary errors in production
- The company’s inventory
Manufacturers should carefully scrutinize each of the above in the lean manufacturing method. The process of going through each component above can seem daunting but requires a pragmatic approach to inspection.
The Kaizen Method
The Kaizen method is often referred to as the Continuous Improvement method. This manufacturing analysis technique comes from Japanese philosophy. The Kaizen method addresses three areas of waste and seeks to eliminate them from the manufacturing process as much as possible.
- Muda (Wastefulness)
- Mura (Unevenness)
- Muri (Overburden)
Some areas companies can identify the above in are ineffective manufacturing processes, excessive or underutilized employees, or excess inventory. The goal of the Kaizen method is to deliver superior value to the end-user or customer.
The Total Quality Management Method
Unlike the methods above, the Total Quality Management method uses a customer-led approach to process improvement. The focus of this method is consistent improvement. This method relies on customer data. Manufacturers use performance metrics to make essential changes that improve the manufacturing process.
Begin Making Changes Now
Manufacturers are not going to compete effectively if they cannot improve their processes. Waste is the byproduct of poor manufacturing processes. There are many options for improvement, including those above.
Companies that are failing should re-evaluate every area of their processes to determine where issues have arisen. Consider the options above, and see which one will work best. Process improvement requires a concerted effort, patience, and time. While they will not help make changes occur overnight, companies will see improvements when they pursue these methods.