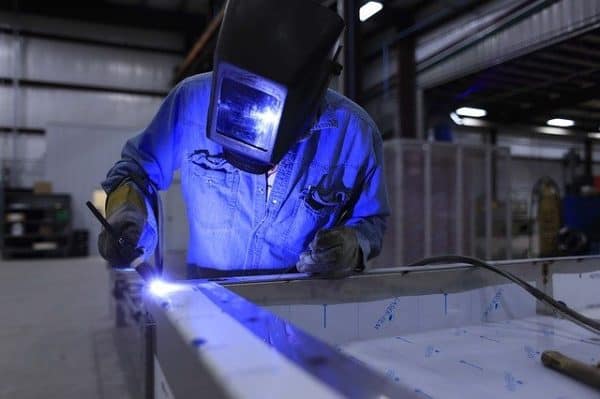
Welding is one of the most critical manufacturing processes across industries – essential for the production of gym equipment, patio furniture, motor vehicles, even smartphones. However, it’s also one of the easiest manufacturing processes to mess up, which can have dire consequences on the safety of your end-product.
If you’ve been struggling with improving your factory’s welding performance, and subsequently, your products’ ultimate quality, there’s only one thing you can do – automate the process.
Welding automation allows factories large and small to enjoy unique benefits that can significantly impact the bottom line. See what you stand to gain from automated welding.
Automated welding is the solution to closing the skills gap
It’s no secret that young people are mainly going for white-collar jobs and trying to avoid trades like welding for fear of them being too labor-intensive without adequate payoff. With the younger workforce shying away from jobs like welding and the older workforce slowly reaching retirement, industries in need of experienced welders are facing a serious talent shortage.
Finding the right people with the right skills and experience is becoming ever-more challenging. The best solution to closing this skills gap is investing in automated welding.
Welding automation started back in the 1960s with General Motors, and it’s only become more sophisticated over the past few decades.
With the top welding machinery, you can ensure that your most critical manufacturing process remains unaffected regardless of how great of a skills gap your industry is dealing with.
It can save you money in the long run
Automated welding can quickly prove to be a hefty initial investment, even if you’re buying the simplest machine. Still, you can rest assured that the investment will pay off sooner rather than later.
You won’t have to slow down your production while searching for the right job candidate, which directly affects your profits. You won’t have to cover the wages, benefits, health insurance, or even professional development costs for your automated team member. Within just a few months, you’ll see the financial benefits of automating your welding processes.
It offers both quality and quantity
If there’s one thing that welding automation offers, it’s consistency. You’ll consistently get work of the highest quality at unprecedented speed.
The automated welders don’t get tired or distracted. They leave no room for human error and work much faster than any employee would, no matter how well-trained they are. If you need to improve product quality and quantity, automated welders will have your back.
You can decrease scrap production
When you automate your welding processes and improve the overall quality of your products, you’ll deal with significantly less scrap.
Considering just how consistent the machine’s output is, you can rest assured that you’ll always receive the type of welding you need – no poor, incomplete welds that lead to breaks and shorten the lifespan of your products. With a perfect weld every time, you’ll throw away less scrap and use up every last piece of the materials you need.
Automated welding brings versatility
You can program automatic welding robots to create any weld you need. You can easily store an array of different settings and welding types and start producing them in an instant – no need to spend time and money on training your staff.
Furthermore, welding isn’t the only thing that these machines can do. Using replaceable end of arm extensions, you can fit the robot with any useful tool – vacuum and pneumatic grippers, drills, paint guns, and sanders, to name but a few. Your welding machine can become as versatile as you need it to.
It increases the overall staff safety
One of the most important reasons you need to make the switch to welding automation is safety. Your human welders are exposed to hazardous conditions throughout their shifts – extreme temperatures, dangerous gasses and flumes, and more. Not to mention that welding can be physically straining, harming your employees and making them more likely to make mistakes.
Automatic welders can reduce your employees’ stress levels and increase the overall safety standards in your factory. The best machines have built-in safety features that shut them down as soon as an error or problem is detected.
You can leave your employees to do safer, more important work that needs a human touch and let your automatic welders take care of the rest.
Final thoughts
Automated welding can benefit any factory, regardless of its size. While it requires a hefty upfront investment, it allows you to cut costs, close the skills gap in your industry, enhance the quality and quantity of your production, decrease scrap waste, and improve the overall safety in the workplace. Test an automatic welder for yourself, and see what a difference it can make.