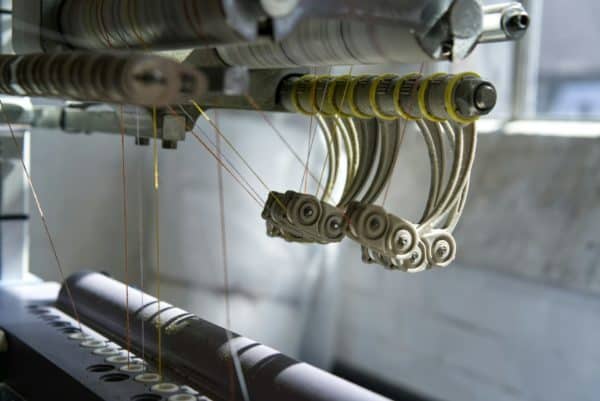
While productivity, efficiency, and profitability are often the measurements we discuss when analyzing our manufacturing plants, none matter without safety.
With as much heavy machinery and hazardous materials as your plant has, you have to make safety a top priority. In doing so, you can reduce downtime and create a more productive work environment for everyone.
Here are six ways you can improve safety at your manufacturing plant.
Regular Training
One of the most effective ways to improve safety at your manufacturing plant is by conducting regular safety training for all employees. This training should cover general safety practices, as well as specific procedures related to the equipment and materials used in your plant.
Start by ensuring that every new employee receives comprehensive safety training before they begin work. This should include information on how to properly operate machinery, handle hazardous materials, and respond to emergencies. Regular refresher courses should also be held for all employees to keep safety protocols fresh in their minds.
In addition to general safety training, consider providing specialized training for certain tasks or roles. For example, employees who work at heights should receive fall protection training, while those handling chemicals should be trained in hazardous material handling.
This sort of training can significantly reduce the risk of accidents and injuries.
Safety Culture
A safety culture is more than just following rules and regulations – even though that’s how we’ve traditionally viewed it. In reality, it’s about fostering an environment where safety is a core value, and everyone takes responsibility for maintaining it.
- Encourage employees to speak up if they notice unsafe conditions or practices, and make sure they feel comfortable reporting safety concerns without fear of retaliation.
- Hold regular safety meetings where workers can discuss potential hazards and suggest improvements.
- Recognize and reward employees who demonstrate a commitment to safety, whether it’s by following protocols diligently or helping to prevent an accident.
Leadership plays a crucial role in shaping the safety culture. Plant managers and supervisors should lead by example, consistently prioritizing safety and reinforcing its importance in every aspect of the operation.
Maintenance of Equipment
Regular maintenance of machinery and equipment is key for preventing accidents and ensuring the safe operation of your manufacturing plant. Equipment that is not properly maintained can malfunction, leading to potentially dangerous situations for workers.
It’s a good idea to establish a routine maintenance schedule for all machinery and equipment, and make sure it’s followed consistently. This includes checking for wear and tear, lubricating moving parts, replacing worn components, and testing safety features like emergency stops and guards.
In addition to scheduled maintenance, encourage workers to report any issues they notice with equipment, such as unusual noises, vibrations, or decreased performance. Addressing these problems promptly can prevent minor issues from becoming major safety hazards.
Safety Products
Having the right safety services and products in place is another important way to protect your workers from the various hazards they may encounter in a manufacturing plant. These safety products are designed to prevent accidents and minimize injuries if an incident does occur.
Here are some essential safety products you should have in place:
- Arc Flash Protection: Protect workers from the dangers of electrical explosions with arc flash suits, gloves, and face shields.
- Eye and Face Protection: Provide safety goggles, face shields, and helmets to protect against flying debris, chemical splashes, and other hazards.
- Fall Protection: Use harnesses, lanyards, and guardrails to prevent falls when working at heights.
- Fire Protection: Make sure fire extinguishers, sprinkler systems, and fire alarms are readily available and properly maintained.
- First Aid/Medical Supplies: Stock your plant with first aid kits, eye wash stations, and other medical supplies to treat injuries promptly.
- Hazardous Material Handling: Use proper storage containers, spill containment systems, and protective gear for handling dangerous chemicals.
- Lockout/Tag Out (LOTO): Implement LOTO procedures to ensure machinery is safely shut down and cannot be restarted during maintenance or repairs.
- Hearing Protection: Provide earplugs or earmuffs to protect workers from excessive noise levels.
- Industrial Hygiene: Monitor air quality and provide respiratory protection to safeguard workers from inhaling harmful substances.
- Gas Detection: Use gas detectors to identify leaks and prevent exposure to toxic or flammable gasses.
- Sorbents and Spill Control: Have materials like absorbent pads and spill containment kits ready to quickly clean up any spills.
Safety Audits
Regular safety audits are necessary for maintaining a safe manufacturing plant. These audits involve systematically reviewing your facility, equipment, and procedures to identify potential hazards and areas for improvement.
You should conduct safety audits on a regular basis, and involve employees in the process. This helps ensure that no safety concern is overlooked and that everyone is aware of the importance of maintaining a safe workplace. After the audit, take action to address any issues that were identified, and follow up to ensure that corrective measures are effective.
Enhance Your Plant’s Safety
Plant safety has to be a top priority for your company this year (and every year). By making it a focus, you can reduce downtime, increase efficiency, and establish a better workplace culture where people feel safe and respected. These six tips are just the start!